塗装剥離、その方法と材料/中外技研(塗装剥離の窓口)
※ダウンロード資料には、塗装剥離の内製化のコストの目安がございます。ご参考にご活用ください。
塗装を剥離する方法は様々なものがあるが、それぞれ特徴があり塗装剥離対象物の材質や表面状態、また塗料の種類によって適切に選択する必要がある。現在の主な塗装剥離の方法について大別し、特徴と適した剥離対象物について解説する。なお、資料ダウンロードには、被塗物の素材に適した塗装剥離剤や剥離内製化例、塗装剥離のコスト等を提供しているので、塗装剥離の参考にして欲しい。
『塗布と塗膜』2024年2月号 特集:治具等の塗膜剥離方法と特徴、並びに塗膜剥離剤と熱分解剥離のメカニズム
なぜ、塗装剥離を行うのか
塗装を行なう企業の多くは、塗装対象物を治具やハンガー、フック等に固定して塗装を行なうため、繰り返し使用する事で治具等に塗装が重ねられ最終的には塗装の不具合を起こす原因となる事がある。このため塗装工程を重ねた治具を廃棄している場合もあるが、廃棄物の削減・リサイクルの観点から塗装を剥離して再利用する事は企業にとって重要なテーマとなりつつある。塗装済み製品も同様の観点から不良品について塗装剥離を行ない再度製品化とすることが増加している。
また既存の剥離設備を稼働している工場ではカーボンニュートラルの観点から、塗装剥離工程のエネルギー消費量を抑える検討も行なわれている。塗装剥離方法には種々の方法があり、それぞれに特徴があるので以下にその方法について記したい。今回はシンナーや単一溶剤にて再溶解・剥離するような塗料種については記載していない。
塗装剥離方法3つの種類とetc...
- 化学的方法
塗装剥離剤を使用して塗膜を分解・軟化・溶解させる。浸漬タイプと塗布タイプがある。
熱的方法
400℃前後に加熱した剥離装置で塗膜を分解・炭化させる。乾留式剥離装置や加熱オーブン剥離装置が代表的なものとなる。
物理的方法
塗膜に対して物理的な力を加えることで塗膜を除去する。ショットブラスト装置や高圧水やサンダーなど。さらに、レーザーを用いた剥離装置などがある。
その他の方法
・塗装治具にメッキ、化学処理を行なう方法
・塗装治具にプレコーティングを行なう方法
・剥離方法を組み合わせて行なう方法
必要な各方法の塗装剥離に関連する技術、設備
化学的方法
様々な塗装剥離剤があり主成分にジクロルメタンを使用した塩素系剥離剤と塩素系溶剤を使用していない非塩素系剥離剤に大別される。対象物と塗膜成分に合った塗装剥離剤を選定することで対象物の素地表面を変化させることなく仕上がるので、精密な治具や製品剥離に適している。法規制や環境負荷の観点から現在の主流は非塩素系剥離剤となっている。
浸漬用塗装剥離剤
塗装剥離剤の専用槽を用意して対象物を浸漬して塗膜を剥離する。非塩素系剥離剤を使用する場合は液温度による剥離性能の差が顕著であることから、一定温度まで加温した状態で剥離を行なうことが多い。加温する際の熱源は電気ヒーターが一般的である。同型状の対象物を剥離する場合は、剥離槽に入れるためのバスケットに加工を行ない効率的に対象物が並ぶようにすることで剥離不良を減らすことが出来る。
<浸漬タイプの一般的な工程>
剥離槽に浸漬→水洗工程→(一時防錆)→乾燥
-1024x768.jpg)
化学的方法(剥離槽)
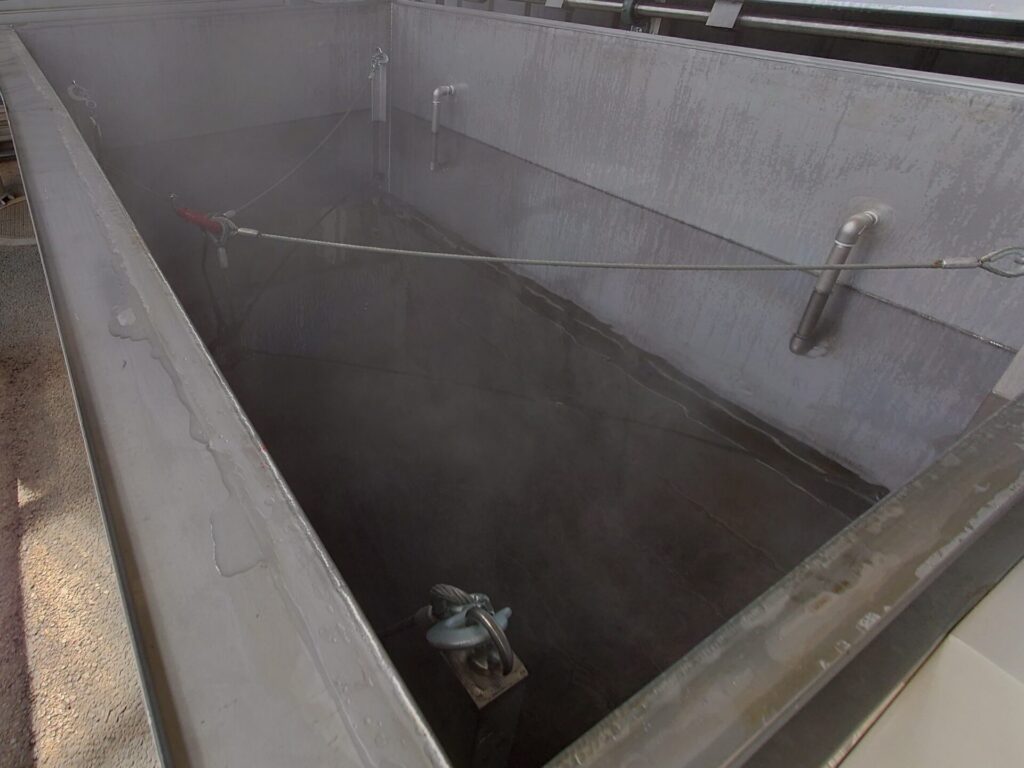
同装置の槽内
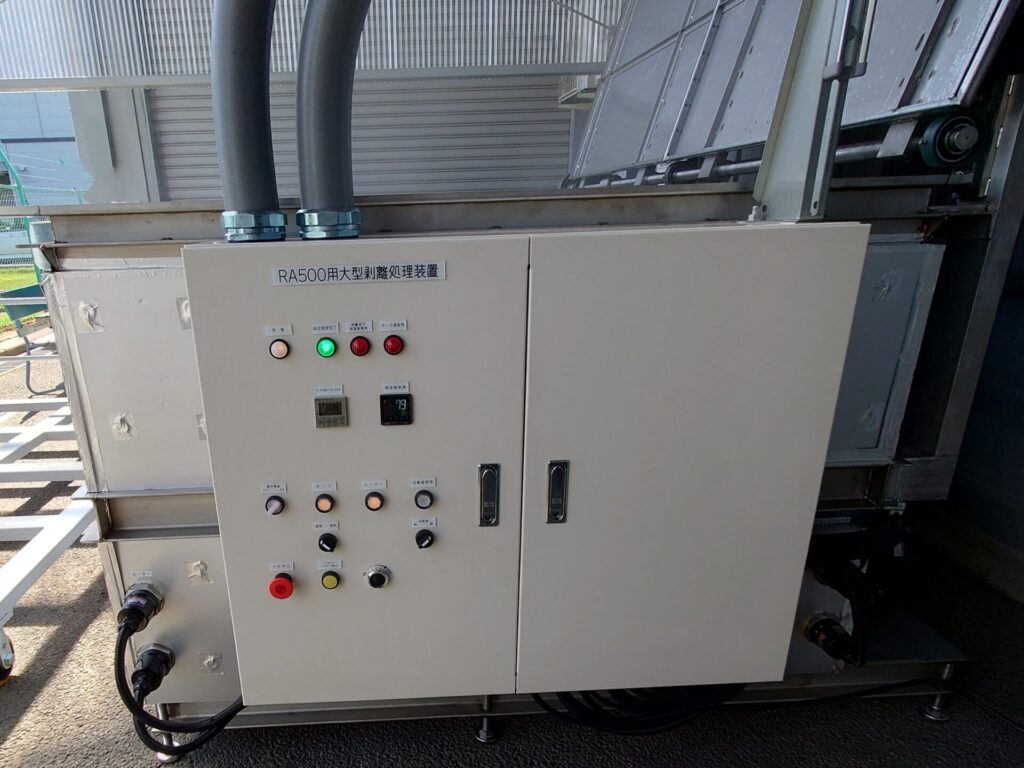
同装置の制御盤
<浸漬で使用する剥離剤の例>
塩素系剥離剤(ジクロルメタン系)の使用方法は、基本的に常温で使用する(ジクロルメタンの沸点39.6℃)。液性は、アルカリ性・中性・酸性。塗料及び剥離対象物の材質によって選定する。メリットとして、剥離性能が高く引火性がない。
デメリットとして、主成分のジクロルメタンの揮発性が高いことから成分組成の変化が起こりやすく剥離剤の精密な成分管理が困難である。また、ジクロルメタンの法規制が厳しく、剥離工程で使用する水洗水中のジクロルメタン除去に高度な廃水処理設備が必要となる(国内該当法規:労安法、PRTR 法、化審法、水質汚濁防止法、大気汚染防止法など)。
一方、非塩素系剥離剤の使用方法は、常温または加温して使用する(常温~90℃程度)。液性は、アルカリ性・中性・酸性。塗料及び剥離対象物の材質によって選定する。メリットは、専用の剥離設備と剥離剤の成分管理を適切に行なうことで安定した剥離性能を維持することができる。剥離工程で使用する水洗水は比較的廃水時の環境負荷が軽い。デメリットとして、剥離性能を維持するために専用の加温槽が必要となることが多い。剥離剤の成分によっては引火性がある。
塗布用塗装剥離剤
塗装剥離剤を増粘させたもので対象物に対して塗布することで塗膜を剥離させる。主成分は塩素系及び非塩素系剥離剤があり主流は非塩素系剥離剤になるが、大型設備等の剥離作業においては加温する事が出来ないため、非塩素系剥離剤で剥離作業を複数回行なう場合や物理的処理などを組み合わせて剥離する方法がある。
熱的方法
乾留式剥離装置
400℃前後に加温した石英砂・珪砂の流動浴に対象物を入れる事で、塗膜中の有機物を分解・炭化させて剥離する。剥離設備は大型容量ものが多く、一度に大量の対象物が処理可能で大型の治具やグレーチングにも対応出来る。しかし、以下の点を注意する必要がある。
・熱による変形の可能性がある対象物には不向きである。
・精密な対象物(可動部分や細かな形状)は変形するおそれがある。
・剥離後の素材表面に微細粒子が付着していることが多いので、次工程でショットブラストやバレル研磨を行なう場合がある。
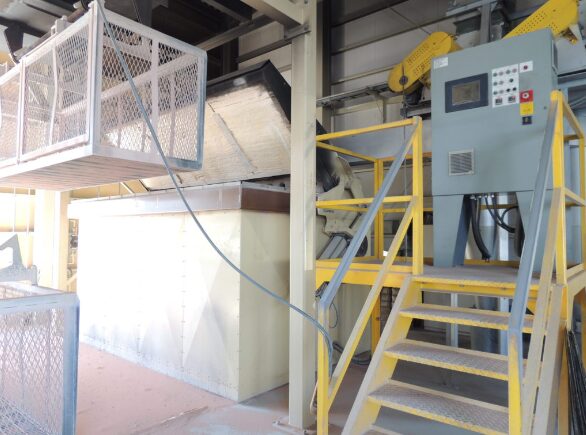
乾留式剥離装置
オーブンタイプ剥離装置
同装置は、剥離装置中をマイクロヒーターやガス等で400℃前後に加熱する事で塗料中の有機物を分解・炭化させて塗膜を剥離する。設備の構造が乾留式剥離設備よりも簡単であるため、設備の大きさに自由度がある。しかし、乾留式剥離装置と異なり対象物に直接触れないため後工程が必要になることが多い。
物理的方法
ショットブラスト装置
同装置は対象物にメディア(鋼製・非鉄金属・樹脂等の球)を衝突させて塗膜を除去する方法である。作業者が手動で操作するものから装置内で対象物を回転させながら自動的に剥離させる大型装置まで、目的に合わせた装置を選ぶことが出来る。メディアを適切に選ぶことで塗装剥離から対象物表面の清浄化など使用範囲が広い等のメリットがある。一方で、メディアが当たらない部分は処理する事が出来ない。未硬化の塗膜が残存している場合は不向きである等のデメリットがある。
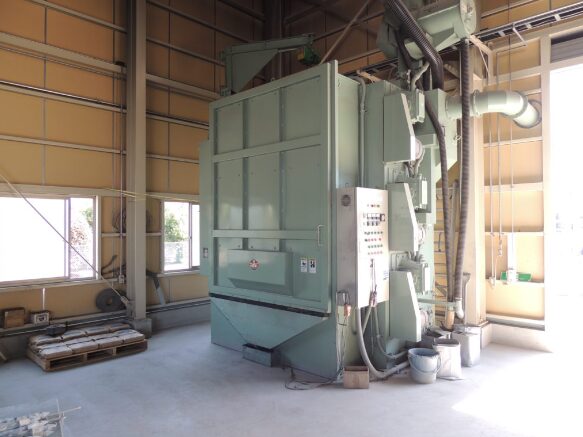
ハンガー式ショットブラスト装置
高圧水やサンダー
簡易な装置で手軽に行なうことが出来る一方で、手作業で行なう場合は大量の処理が難しい。
レーザーを用いた剥離装置
レーザー光により塗膜や錆を除去する方法である。レーザー出力を調整する事で塗膜厚さに合わせる事が可能であるが素材を傷めない程度にする必要があることと、塗装治具など塗膜厚みがある場合は時間がかかる。
例として800×600mm サイズの平面治具で膜厚800~1500μmの場合、片面60分程度を要した。対象物にレーザー跡が残る場合もある。作業の自動化が可能で無人で剥離作業を行なうことが出来るメリットがある。
その他の方法
塗装治具にメッキ、化学処理を行なう方法
塗装剥離技術とは間接的な関係になるが、塗装剥離作業を簡便にする事を目的にした手法である。塗装治具にメッキや表面処理を行なう事で剥離作業時に時間等を短縮する事ができる。
塗装治具にプレコーティングを行なう方法
塗装治具に事前に剥離剤で安易に除去出来るプレコーティングを行なう事で、剥離作業時に時間・手間を短縮する事が出来る。
剥離方法を組み合わせて行なう方法
塗装剥離加工を専門に受託している会社の場合は、既出の剥離方法を2種類以上組み合わせることで塗装剥離を行なう場合もある。組み合わせは以下がある。
・塗装剥離剤を2種類以上使用
・オーブンタイプ剥離装置+ 塗装剥離剤
・乾留式剥離装置+ ショットブラスト装置
・塗装剥離剤+ ショットブラスト装置 など
塗装剥離工程の後処理
塗装剥離後は対象物の材質によって、素材表面が変色する場合があるので、必要に応じて化学研磨剤を使用する場合がある。また塗装剥離後に鋼製の対象物を保管する場合は、発錆する可能性があるため一時防錆処理を行なう事が多い。一般的な防錆処理剤として防錆油、水溶性一時防錆剤、気化性防錆紙、気化性防錆フィルム、乾燥剤などがある。
中外技研の紹介
中外技研では塗装剥離剤を含む化学工業薬品メーカーであるが、塗装剥離専門会社、設備会社等と協業して、塗装剥離作業の全般を提案できる「塗装剥離の窓口」を展開している。塗装剥離の窓口のホームページには、塗装剥離剤の事例一覧を紹介している。
塗装工場内で剥離設備を導入したい場合や塗装剥離を外部に委託したい場合など、塗装剥離全般について最適な方法を提案している。塗装剥離剤を導入した工場には導入後も塗装剥離剤の保守管理、剥離作業方法のアドバイスや関連備品の提案などアフターフォローも含めたサービスを行なっている。
まとめ
以上のように塗装剥離を行なうためには種々の方法があるが、実際には剥離対象物に合わせた細かな作業方法等を工夫することが重要である。塗装剥離専門会社においては複数の剥離工程を組み合わせるなどの知見を持っている。企業の塗装工場に剥離設備を導入する場合は塗装剥離方法や種類の特徴を理解した上で選定することも重要であるが、塗装剥離工程の作業・運用方法についても同様に重要となる。本稿により塗装剥離方法の選択の参考となれば幸いである。
=================
著者:長 健太郎(Choh Kentaro)
株式会社中外技研 代表取締役
化学工業会社の研究職として有機合成、界面活性剤等の配合・乳化技術、塗装剥離剤、洗浄剤、防錆剤等の開発に従事した後、2013年4月に(株)中外技研を設立、現在に至る。
================
中外技研(塗装剥離の窓口) ダウンロード用資料目次
1.剥離剤のスペック表+こんな被塗物にはこの薬剤!
・被塗物の素材に適した塗装剥離剤
・塗装剥離剤のスペック表
2.剥離ができない!組み合わせによる剥離方法で課題解決!!
・組み合わせによる剥離方法の事例
3.剥離を内製しよう!低コストでもできる簡単な剥離設備!
・まずは社内で剥離してみよう
・社内で多くの製品・治具剥離などをおこないたい(加温式剥離槽(100~300L))
・小型剥離層
4.剥離のコストとは!気になる塗装剥離の費用
・塗装剥離のコストとは